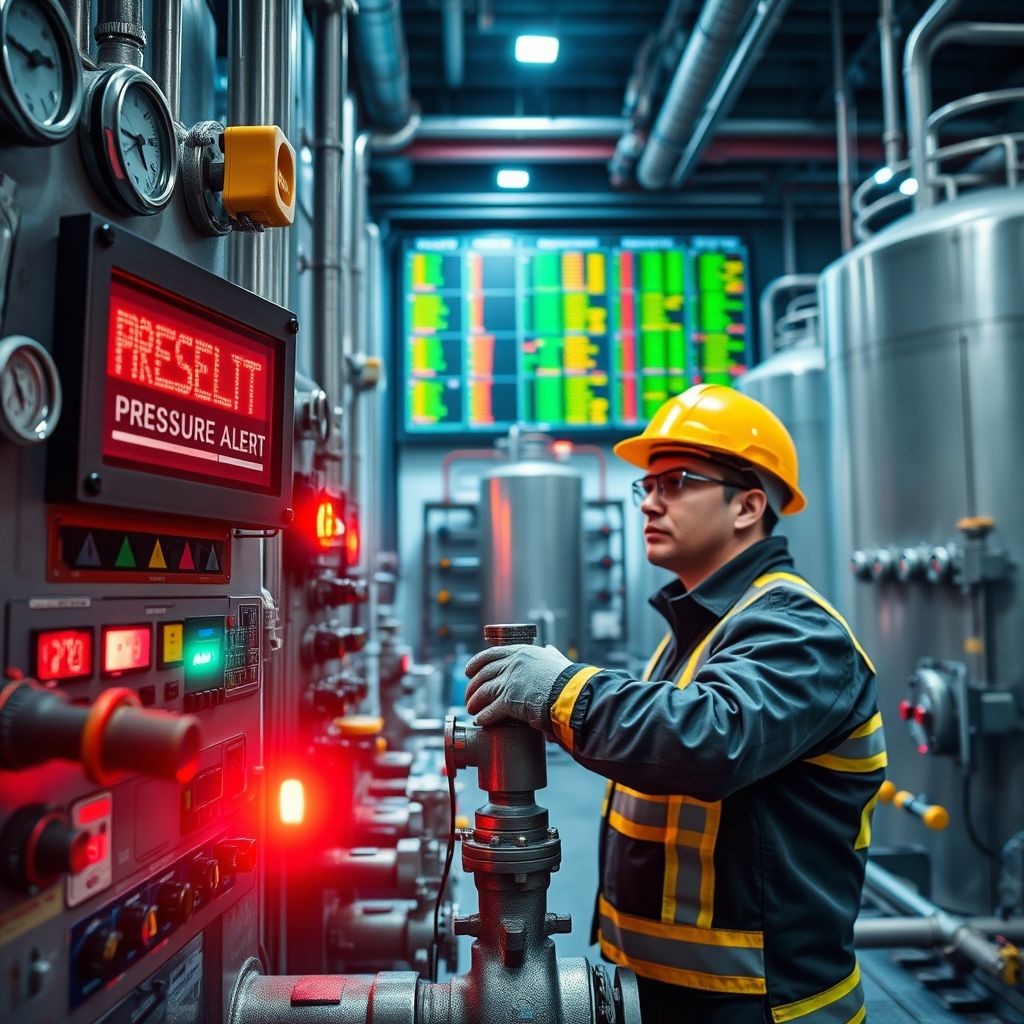
Boom! A pressure valve blows, sending a deafening screech through the facility. Workers scramble. A red warning light flashes, but it’s already too late—the system has suffered catastrophic failure. Thousands of dollars lost. Equipment damaged. Safety compromised.
Now, imagine a different scenario. A pressure alarm system catches the spike early. An alert sounds. Operators react in seconds, adjusting the system before disaster strikes. Business as usual. No costly downtime. No safety violations.
Pressure alarms aren’t just another industrial add-on—they’re the unsung heroes of operational safety. But integrating them into an existing system? That’s where things get tricky. Where do you start? How do you ensure compatibility? What about compliance in hazardous environments?
This guide isn’t just about the “what”—it’s about the “how” and the “why.” From oil refineries to pharmaceutical cleanrooms, pressure alarms save lives, prevent disasters, and keep industries running smoothly. Buckle up—because we’re diving deep into the world of pressure alarm integration.
Understanding Pressure Alarm Systems
What is a Pressure Alarm System?
At its core, a pressure alarm system is a silent sentinel, constantly monitoring pressure levels in pipelines, tanks, reactors, and HVAC systems. When things go south—pressure spikes or drops—the system triggers an alert, forcing immediate action. Think of it as an industrial heartbeat monitor.
Without these systems, operators are flying blind. The stakes? Explosions. Leaks. Regulatory fines. Even loss of life.
How Pressure Alarms Are Used in Different Industries
1. Oil and Gas:
A pipeline rupture isn’t just a costly inconvenience—it’s an environmental disaster waiting to happen. Pressure alarms detect leaks and prevent catastrophic failures in offshore rigs, refineries, and gas processing plants.
2. Chemical Processing:
Reactor vessels operate under extreme conditions. One uncontrolled pressure spike could trigger a chain reaction, leading to toxic leaks or even explosions. Pressure alarms provide early intervention before a minor fluctuation turns into a crisis.
3. Manufacturing:
Hydraulic presses, pneumatic actuators, and injection molding machines all depend on stable pressure. Too high? Equipment fatigue. Too low? Product defects. Pressure alarms keep the production line moving, ensuring quality and efficiency.
4. Pharmaceuticals & Food Processing:
Ever wondered how cleanrooms stay contamination-free? They rely on precise air pressure differentials. A drop in pressure allows unfiltered air to enter, risking contamination. Pressure alarms ensure sterility is never compromised.
5. Power Plants:
Steam turbines demand precision. Too much pressure and a boiler could explode; too little and efficiency tanks. A well-integrated pressure alarm system balances power generation and safety, avoiding costly shutdowns.
Types of Pressure Alarm Systems & How to Choose the Right One
Not all pressure alarms are created equal. Selecting the right one means understanding their technology, strengths, and limitations.
1. Mechanical Pressure Alarms
- Best for: Steam boilers, hydraulic presses, and legacy systems.
- How They Work: Uses a diaphragm, bellows, or Bourdon tube to activate a mechanical switch when pressure crosses a set threshold.
- Key Considerations: No power needed. Reliable. Simple. But lacks remote monitoring.
2. Electronic Pressure Alarms
- Best for: Automated industrial plants, precision manufacturing, and digital safety systems.
- How They Work: Uses strain gauge or piezoelectric sensors to measure pressure electronically, feeding data into PLCs and SCADA systems.
- Key Considerations: Highly accurate, integrates with digital networks, but vulnerable to power failures without backup.
3. Wireless Pressure Alarms
- Best for: Remote sites, mobile operations, and large industrial campuses.
- How They Work: Sends data via Wi-Fi, Bluetooth, or LoRaWAN, enabling remote monitoring from a control room or even a smartphone.
- Key Considerations: No messy wiring. Scalable. Flexible. But beware of signal interference in heavy industrial zones.
4. Multi-Parameter Pressure Alarms
- Best for: High-precision industries like chemical processing and energy production.
- How They Work: Monitors pressure, temperature, and flow rate simultaneously.
- Key Considerations: AI-driven analytics, predictive maintenance capabilities—but costlier and complex to set up.
Step-by-Step Guide to Integration
Step 1: Assess the Infrastructure
- Identify pressure-sensitive points: Pipelines, storage tanks, compressors, and reactors.
- Determine compatibility with existing SCADA, PLCs, or BMS systems.
Step 2: Select the Right Sensor Type
- Strain Gauge: Best for high-pressure environments.
- Piezoelectric: Fast response time for hydraulic and pneumatic applications.
- Capacitive: Ideal for low-pressure HVAC and cleanroom environments.
Step 3: Configure Alarm Logic
- Latching Alarms: Requires manual reset—ideal for critical failures.
- Non-Latching Alarms: Resets automatically—best for real-time monitoring.
- Dual-Threshold Alarms: Warns at different levels—prevention before escalation.
Step 4: Test and Calibrate for Accuracy
- Zero Calibration: Ensures baseline accuracy at no pressure.
- Span Calibration: Adjusts sensor output for maximum pressure.
- Real-world testing: Simulate failures before going live.
Step 5: Train Personnel on Usage & Maintenance
- Establish response protocols—who does what when a pressure alarm triggers?
- Conduct routine drills to ensure familiarity with the system.
Troubleshooting Common Issues
1. False Alarms
- Cause: Sensor drift, electrical noise, poor threshold settings.
- Solution: Regular recalibration, proper shielding, and threshold fine-tuning.
2. Signal Interference in Wireless Pressure Alarms
- Cause: Electromagnetic noise from heavy machinery.
- Solution: Use shielded cables, relocate sensors, or switch to wired backups.
3. Alarm Fails to Trigger
- Cause: Wiring faults, sensor malfunctions, software delays.
- Solution: Check for loose connections, faulty relays, or misconfigured PLC settings.
Installing Pressure Alarms in Hazardous Environments
Some workplaces come with explosive risks—oil refineries, chemical plants, and gas pipelines. A standard pressure alarm won’t cut it.
Best Practices for Intrinsically Safe (IS) Installations
- Use ATEX-certified pressure sensors in hazardous locations.
- Install IS barriers to prevent electrical sparks in explosive atmospheres.
- Deploy redundant alarms—one failure must not lead to disaster.
Conclusion
Pressure alarms aren’t just safety devices—they’re business savers, compliance enforcers, and efficiency boosters. Whether you’re managing a gas pipeline, a pharmaceutical plant, or a factory floor, the right pressure alarm system can mean the difference between smooth operations and costly shutdowns.
So here’s the real question: Are you prepared, or are you waiting for a crisis to force your hand? The time to integrate pressure alarms is now—before an emergency does it for you.